March 02, 2023
How to Prepare When Converting to ASTEC Digital’s Asphalt Plant Controls
Find out how calibration affects mix design, and how our plant automation systems help so many operators improve their mix.
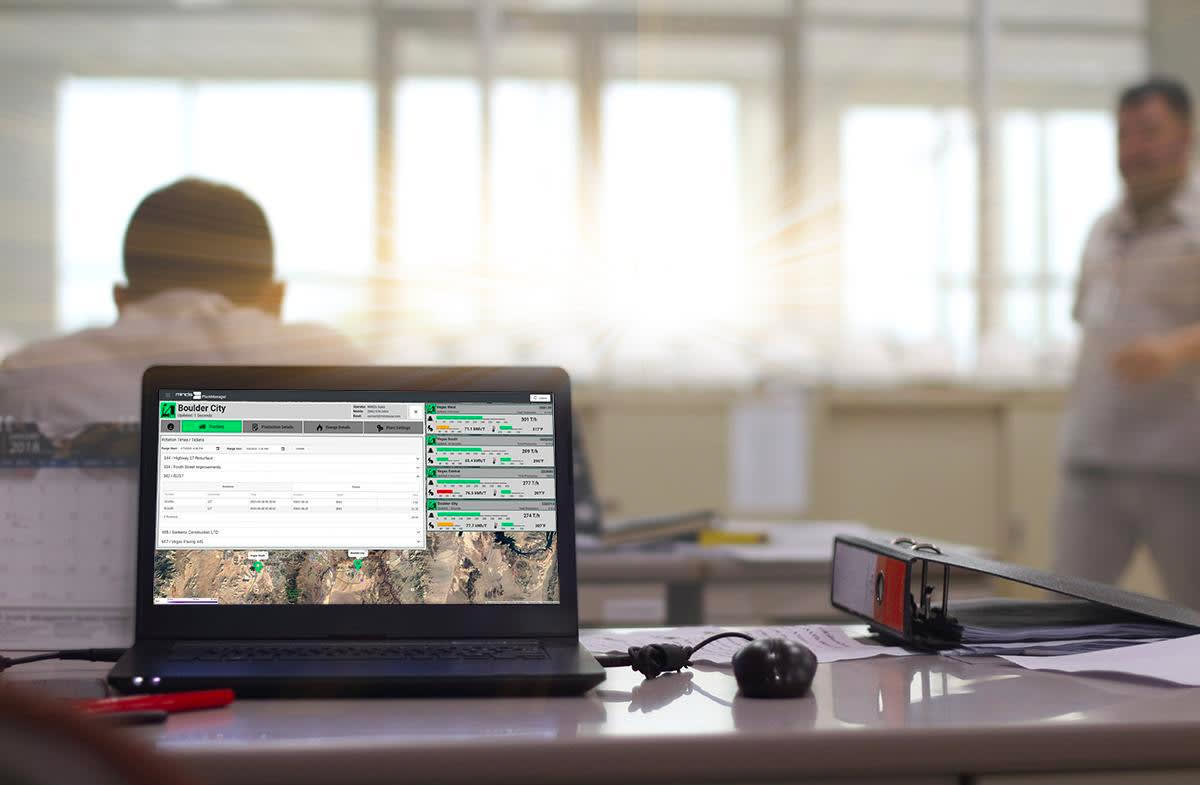
Plant managers start to see improvements to the asphalt production process immediately after installing ASTEC Digital’s asphalt plant software.
“Forget everything you used to know,” says McGaughey, ASTEC Digital’s Director of U.S. Operations. “That’s my number one thing I like to tell plant operators before we start commissioning.”
It might sound intimidating, but it’s actually exciting. Installing ASTEC Digital’s reliable, accurate and customizable asphalt plant software suite is a transformational experience that gives plant operators the level of fine-tuned automation and control they need to get the most out of their plants. We spoke with McGaughey about what plant operators need to know about the conversion process and how to make it particularly successful.
Up-front considerations
The first question McGaughey says plant operators should ask themselves is what their end goal is. “Do you want to keep your plant running for five, 10, 20, 30 years? That determines what level of industrial automation and change that should be provided,” he says. “We’ll make recommendations to our customers based on their goals.”
The environment is a plant—and its future control system—is operating as a critical factor for the installation.
While some plants have done a good job from the beginning by setting up their existing plant control system in a climate-controlled environment indoors, others have their control boxes “mounted on the side of a plant out in the field,” McGaughey says. “They blow air out through filters that don’t get maintained, they’re in a dusty environment, the control panels are dirty, and dust runs into the air stream until they quit working.”
For that reason, it is important for ASTEC Digital to understand the environment the plant’s operating within and the state of your equipment. Older or poorly maintained equipment, for example, may impact how successful the plant automation process is. “If the equipment has been in service since 2004, for example, and it has been outdoors, those are factors. The condition of the equipment will affect how hard the installation is,” he says. “For a customer to be happy with all aspects of the plant automation, we may recommend they make some changes.”
McGaughey advocates for plant operators to have their new ASTEC Digital asphalt plant controls installed in a controlled environment designed for occupancy, with air conditioning and/or heat for consistent temperature and no possibility of precipitation getting in.
Customizing the Software
The first step of the installation process is a plant audit. The plant manager will identify all the equipment that they want to be controlled by ASTEC Digital’s plant automation software, particularly any equipment that has previously been manually controlled. They’ll also need to decide how much automation they actually want. McGaughey notes the level of automation greatly varies depending on what devices and sensors each customer has.
Once ASTEC Digital has the results of the plant audit, a member of the company’s design team will create a graphic mockup of the plant layout, which plant operators will see when they use the plant software.
“Each plant is customized visually for what the plant actually looks like,” McGaughey says.
Where it can get complicated is how each plant handles bag-house fines, which is highly individual. “There are so many paths to getting it back into the system, but we have all the possibilities handled,” he says. “Some people have very customized plants, but that is exactly where our system excels — it is even better in those situations where the contractor has such a custom plant that typical out-of-the-box controls will not plug and play. We have a company that specializes in writing software that has the flexibility to handle those needs.”
Out with the Old
When it is time to install, plant managers can choose to do it themselves or have one of ASTEC Digital’s authorized factory resellers handle the process.
Retrofitting the plant by taking out existing controls and implementing ASTEC Digital’s system from scratch with the new XIO will take around three to four weeks, McGaughey says. Plant operators need to first remove the existing system and ensure their wiring is labelled correctly — a process that he says can take multiple days depending on how well the plant’s control systems were taken care of. Then, they should ensure all their devices are turned off to install the new plant control system and rewire it to the operation’s equipment.
This could take longer if plant managers further upgraded their plants with new equipment. While that process is slow, training operators on the new system is speedy. In McGaughey’s experience, plant operators catch on to ASTEC Digital’s intuitive plant control system within two or three days. “Around that time, they’re perfectly comfortable doing whatever they need to do,” he says. “That’s one of the major benefits of our system.”
If plant operators have any questions afterward, ASTEC Digital offers 24/7 online support.
Immediate Payoff
Plant managers might expect to wait weeks or months to see the benefits of their new plant software — but McGaughey says customers start to see improvements to the asphalt production process immediately. You see a reduction in plant calibration time, your mix is in the specification of the blend, and barring outside uncontrolled issues and all those legacy issues tend to get resolved,” he says. “And as managers learn the Plant Operations Manager dashboard, they’re able to tighten up and run their operations better.”