March 02, 2023
Streamline the Asphalt Production Process with PlantManager
How ASTEC Digital’s Plant Operations Manager asphalt plant software helps operators and managers get a birds-eye view of their plant.
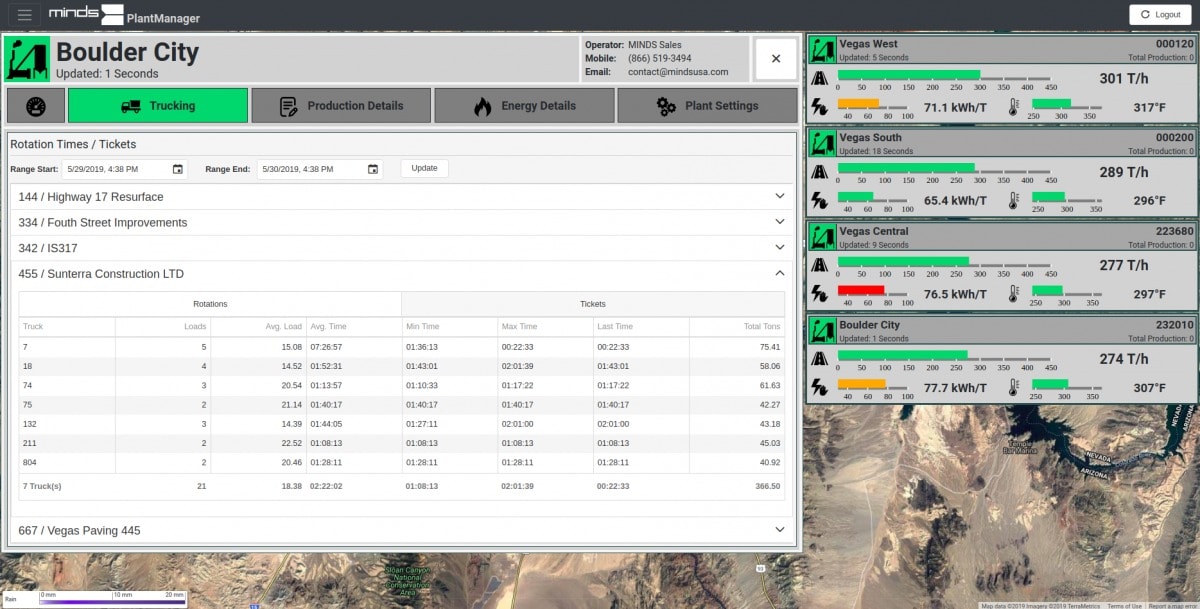
Asphalt operations managers only see what their plants are doing when they are physically at the plants, while asphalt plant operators have always had access to the data that they need to run their plants. If operations managers wanted to see what was happening, it was typically scattered across several applications and not what was happening in real-time. That made it challenging to have a clear overview of how well the plant was operating and whether they could make changes to improve efficiency. That's where ASTEC Digital's Plant Operations Manager comes in.
Mark McGaughey, ASTEC Digital’s incoming Director of US Operations and a former maintenance manager of Milestone Contractors LP's asphalt plants, talks about the benefits of the PlantManager system, having worked with it as an ASTEC Digital customer.
Q: What is PlantManager, and what does it do?
A: PlantManager is a dashboard dedicated to what you need to manage plant operations. It shows in real-time all the data and controls a plant operator or manager would need. The PlantManager shows everything from the product you're producing and the tons per hour at which it's being produced. It shows the mix temperature and binder replacement percentage. Also, the moisture content is all catalogued and recorded. PlantManager includes data on sales tickets, HMA silo inventories, asphalt tank inventories, and what products are in the A/C tanks. It's a single access point to see everything happening at the plants.
Q: Have you seen an uptake in interest and adoption of PlantManager within the industry?
A: Definitely. Once the managers see that they're able to get real-time data that they need from now, three days, a week, or a year ago without going into two or three different systems, they're immediately on board. Before PlantManager, we had multiple systems you had to log into to get data from to understand what the sales and production info was, or you would have to call the accounting department to get a report. But, everyone knows that ship had already sailed. People like the fact that they have a single point of entry to see everything at the plant that's happening now.
Q: What are some new PlantManager features that have been most beneficial for plant operations?
A: The ability to have most fuel flow meters connect to the plant control system and display an instant, as well as the totalized energy used per ton, is a game-changer. For example, the Therms per ton (configured to any unit desired) for energy usage to dry our aggregates and produce mix are all on the dashboard in real-time. The operators, as well as the managers, can see what is required to dry the aggregates and RAP. The display on the PlantManager dashboard shows the best theoretical calculation possible based on several factors: ambient temperature for the last 72-hour average for your location, composite moisture for aggregates, and recycling. It's kind of like the dashboard in your vehicle; based on your driving habits, you're improving or reducing your miles per gallon. That input is going to be there for plant operators/ managers, and I think that will help reduce the cost of their operations.